Testing Profinet: The Basics
March 24, 2021 / General, 101 learning, Installation and testing, Industrial Networks, Best Practices
We all know by now that Ethernet has infiltrated the factory floor as the communication protocol of choice for exchanging data between devices and controllers, with applications like Modbus, EtherCat, EtherNet/IP and Profinet that are all based on Ethernet. The two leading applications—EtherNet/IP and Profinet together account for about 60% of the market, as both excel in supporting deterministic communication for real-time data and control.
As industrial Ethernet continues to gain ground with the adoption of IIoT, Profinet is a popular choice primarily due to its integration with Profibus-based fieldbus integration at the I/O field level and faster speeds. At the same time, new technologies on the horizon like Single-Pair Ethernet and Advanced Physical Layer may end up better fulfilling the goal of bringing Ethernet down to the field level in industrial environments.
But since Profinet links continue to grow throughout the industrial control and SCADA networks, it helps to know how to test them.
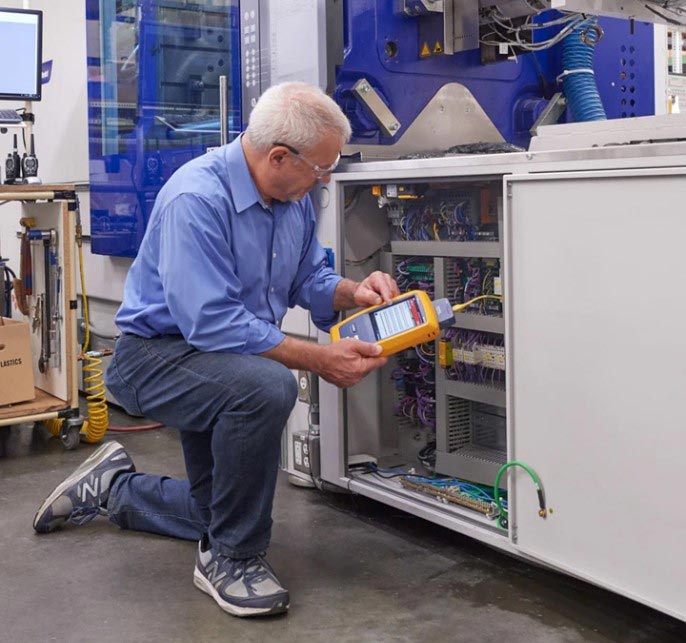
Profinet vs. Ethernet
The difference between Profinet and Ethernet is best understood by referring to the ISO “seven layer” model. Profinet is NOT Ethernet – it is a Layer 7 application just like HTTP, the language used for website traffic on the Internet. Layer 7 is what provides functionality for Profinet closest to the user and determines resource availability. Ethernet is, by contrast, a Layer 2 technology where information is sent and received from one device to another using media access control (MAC) addresses that are part of an Ethernet frame and Layer 1 that includes the physical media needed for transmission (i.e., cables and connectors). Profinet is, at layer 7, based on Ethernet at Layers 1 and 2, so in essence they are complementing technologies rather than competing technologies.
Profinet is supported by Ethernet components, however, standard commercial-grade components cannot stand up to the rigors of the industrial environment. While some light industrial Profinet installations may be supported by hardened RJ-45 connectors, it’s more common to see the use of M-series locking thread connectors like the 4-pin (2-pair) M12 D-coded connector for up to 100 Mb/s and 8-pin (4-pair) M-12 X-coded connector for up to 10 Gb/s. The cables are also typically shielded (either F/UTP or S/FTP) to prevent interference from industrial equipment and they feature more robust jacketing materials than standard polyvinyl chloride (PVC) jacketing used for commercial-grade cables. For example, cables used in industrial Profinet deployments might feature fluorinated ethylene polypropylene (FEP), thermoplastic elastomer (TPE) or polyurethane (PUR) jacketing that offer better resistance to temperature extremes, chemicals, abrasion and other industrial environment elements.
Profinet Cable Testing is Ethernet Cable Testing
Since Profinet uses category Ethernet cables, you’re going to test them in a similar manner per the requirements of the cable category you’re using. Like commercial Ethernet, Profinet is limited to 100 meters so you’re going to test for length. Since more than half of Industrial Ethernet problems can be traced to cabling, testing Profinet should also include basic wiremap testing to test for continuity and problems like opens, shorts, reversed pairs, crossed pairs and split pairs. You’re also going to test for internal crosstalk (i.e., NEXT, ACR-F, PS ACR-F, etc.), as well as alien crosstalk if using Category 6A.
Be Sure to Select the Correct Limits When Testing Profinet
When selecting limits for testing Profinet links, first and foremost, you need to follow the recommendations of your machine and cabling supplier and your automation equipment vendor. But you’re most likely going to be testing to either TIA-1005-A standards for North America or ISO/IEC 11801-3 standards for International based on the category or class of cable used.
While the Fluke DSX CableAnalyzer includes channel test limits for Profinet, which can be found in the “Application” group, it is often recommended to test Profinet to newer end-to-end (E2E) limits based on ISO 11801-9902 that includes the performance of the mated pairs at either end, and will be integrated into the next edition of 11801-3. In industrial deployments, it is common to see cables field terminated to eliminate slack, and often the cables are used in point-to-point links without cross-connections or interconnects. Since channel testing does not include the performance of the plugs at either ends, there is no way to know if the field-installed connectors will support the application using channel limits. However, E2E limits include testing the end connectors, ensuring those field installed plugs are properly tested and that the point-to-point connection will perform.
Profinet Cable Testers – What to Look for
Here are some things to consider when shopping for a Profinet cable tester:
- Test limits for Category, Profinet and End to End links
- Ability to certify to industrial (MICE) Electromagnetic cable specifications
- Support for industrial connectors: M8, M12-D, M12-X
- Endorsement by leading industrial cable suppliers
- Ability to pinpoint simple or complex cabling problems quickly
- Rugged and reliable
- Support: online, phone, service
Our DSX CableAnalyzer Series supports all the appropriate Industrial Ethernet certification limits and connector types and is endorsed by more than 30 leading cable manufacturers. Its unique Fault Info feature displays the location of simple faults (breaks, bad connectors) along with complex ones (such as water in the cable). And it comes in a Fluke-rugged package, ready for daily use.